Below information is from OSHA's
website. Please read carefully
to install and operating any robots and any machine for your production
line.
Guidelines for Robotics Safety
U.S. Department of Labor
Occupational Safety and Health Administration
OSHA Instruction PUB 8-1.3 SEP 21,1987 Office of
Science and Technology Assessment
FOREWORD
The purpose of this instruction is to inform OSHA
compliance officers and employers and employees about safety concerns
that have arisen with the growing use of robotics systems in
manufacturing. Industrial robots can be used to perform hazardous tasks
but in doing so they can create new hazards. With the burgeoning use of
robots in industry, it is feared that without adequate guarding and
personnel training, injury rates for employees working with robots may
increase.
Current guidelines for robot safety include the
American National Standards Institute (ANSI) ANSI-RIA R15.06-1986,
"American National Standard for Industrial Robots and Robot Systems -
Safety Requirements," and the National Institute for Occupational Safety
and Health (NIOSH) December, 1984 Alert "Request for Assistance in
Preventing the Injury of Workers by Robots." Copies of the ANSI Standard
are available from the American National Standards Institute, Inc., 1430
Broadway, New York, NY 10018. The NIOSH Alert was prepared by its
Division of Safety Research, 944 Chestnut Ridge Road, Morgantown, WV
26505.
This instruction provides general introductory
material describing the features of robots and robotics systems which
present unusual hazards and will describe some of the more common safety
systems employed to alleviate these hazards. The ANSI Standard defines
consensus provisions for the construction, reconstruction, modification,
installation, safeguarding, care, testing, and start-up of robots and
robotics systems as well as training for robot and robotics systems
operations and maintenance personnel. The NIOSH Alert contains safety
recommendations that are based on its field evaluation of the first
identified robot-related fatality in the United States.
INTRODUCTION
Robots are reprogrammable, multifunctional, mechanical
manipulators that typically employ one or more means of power:
electromechanical, hydraulic, or pneumatic. Industrial robots have been
used chiefly for spray painting, spot-welding, and transfer and assembly
tasks. A robot performs its tasks in a physical area known as the robot
operating work envelope. This work envelope is the volume swept by all
possible programmable robot movements. This includes the area where work
is performed by robot tooling.
A robot can have one or more arms which are
interconnected sets of links and powered joints. Arms are comprised of
manipulators which support or move wrists and end-effectors. An end-effector
is an accessory tool specifically designed for attachment to a robot
wrist to enable the robot to perform its intended task. Examples of
end-effectors include grippers, spot-weld guns, and spray paint guns.
The ANSI R15.O6-1986 Standard defines an industrial robot system as that
which includes industrial robots, end-effectors, and any equipment,
devices and sensors required for the entire robot system to perform its
tasks.
A-2
OSHA Instruction PUB 8-1.3 SEP 21, 1987 Office of
Science and Technology Assessment
Most robots are set up for an operation by the
teach-and-repeat technique. In this technique, a trained operator
(programmer) typically uses a portable control device (commonly referred
to as a teach pendant) to manually key a robot and its tasks. Program
steps are of the up-down, left-right, in-out, and
clockwise-counterclockwise variety. Robot speeds during these
programming sessions are required to be slow. The ANSI Standard
currently recommends that this slow speed should not exceed 10 in/sec
(250 mm/sec).
The very nature of robotics systems operations has
introduced a new type of employee into the industrial workplace, the
corrective maintenance worker. This individual is normally present
during all operations of a robotics system and is responsible for
assuring continuing operation - adjusting speeds, correcting grips, and
freeing jam-ups. The corrective maintenance worker may also be the
trained programmer who guides a robot through the teach-and-repeat
technique. It is necessary for this individual to be near the robot from
time to time, which raises concerns about his or her safety and the
safety of other workers who may also be exposed.
Recent studies in Sweden and Japan indicate that many
robot accidents do not occur under normal operating conditions but
rather during programming, adjustment, testing, cleaning, inspection,
and repair periods. During many of these operations, the operator,
programmer or corrective maintenance worker may temporarily be within
the robot work envelope while power is available to moveable elements of
the robot system.
This guideline describes some of the elements of good
safety practices and techniques used in the section and installation of
robots and robot safety systems, control devices, robot programming and
employee training. A comprehensive list of safety requirements is
provided in the ANSI R15.06-1986 Standard.
TYPICAL ACCIDENTS
The following are documented accidents involving
robots that occurred recently in Japan, Sweden, and the United States:
- A worker attempted to remove an imperfectly
formed piece from a conveyor with both hands while the
operation limit switch of a material feed and removal robot
remained in its active position. The worker's back was
forced against the robot.
- After adjusting a metal shaving machine, an
operator was caught between the machine and a just-extended
arm of a material feed and removal robot.
A-3
OSHA Instruction PUB 8-1.3 SEP 21, 1987 Office of
Science and Technology Assessment
- A welding robot went functionally awry and
its arm flung a worker against another machine.
- A worker removed the cover of an operating
assembly robot to retrieve a fallen part and caught his hand
in the robot's drive train.
- A worker attempted to retrieve a part
needed in an ongoing assembly without shutting off an
assembly robot's power supply. His hand was caught between
the robot's arm and the unit being assembled.
- A robot's arm functioned erratically during
a programming sequence and struck the operator.
- A fellow employee accidentally tripped the
power switch while a maintenance worker was servicing an
assembly robot. The robot's arm struck the maintenance
worker's hand.
- An operator performing troubleshooting on a
metal plater robot maneuvered the robot's arm into a stopped
position. This triggered the robot's emergency stop mode
which delayed venting of a pneumatic air storage device.
When the return mode was activated, the robot's arm moved
suddenly and jammed the operator's thumb against a
structural member.
- An automatic welder robot operator made a
manual adjustment without stopping the robot. He was hit in
the head by one of the robot's moving parts when the next
batch of weldments arrived.
- A materials handling robot operator entered
a robot's work envelope during operations and was pinned
between the back end of the robot and a safety pole.
SAFETY SYSTEMS
The proper selection of an effective robotics safety
system must be based on hazard analysis of the operation involving a
particular robot. Among the factors to be considered in such an analysis
are the task a robot is programmed to perform, the start-up and the
programming procedures, environmental conditions and location of the
robot, requirements for corrective tasks to sustain normal operations,
human errors, and possible robot malfunctions. Sources of robot hazards
include:
1. Human errors;
2. Control errors;
3. Unauthorized access;
4. Mechanical hazards;
5. Environmental hazards; and
6. Electric, hydraulic, and pneumatic power
sources.
A-4
OSHA Instruction PUB 8-1.3 SEP 21, 1987 Office of
Science and Technology Assessment
An effective safety system protects operators,
engineers, programmers, maintenance personnel, and others who could be
exposed to hazards associated with a robot's operation. A combination of
methods may be used to develop an effective safety system. Redundancy
and backup systems are recommended, particularly if a robot can create
serious hazardous conditions.
Guarding Methods:
1. Interlocked Barrier Guard
This is a physical barrier around a robot work
envelope incorporating gates equipped with interlocks. These
interlocks are designed so that all automatic operations of the
robot and associated machinery will stop when any gate is
opened. Restarting the operation requires closing the gate and
reactivating a control switch located outside of the barrier. A
typical practical barrier is an interlocked fence designed so
that access through, over, under, or around the fence is not
possible when the gate is closed.
2. Fixed Barrier Guard
A fixed barrier guard is a fence that requires
tools for removal. Like the interlocked barrier guard, it
prevents access through, over, under, or around the fence. It
provides sufficient clearance for a worker between the guard and
any robot reach, including parts held by an end-effector, to
perform a specific task under controlled conditions.
3. Awareness Barrier Device
This is a device such as a low railing or
suspended chain that defines a safety perimeter and is intended
to prevent inadvertent entry into the work envelope but can be
climbed over, crawled under, or stepped around. Such a device is
acceptable only in situations where a hazard analysis indicates
that the hazard is minimal and inter locked or fixed barrier
guards are not feasible. Interlocked or fixed barrier guards
provide a positive protection needed to prevent worker exposure
to robotic systems hazards.
4. Presence Sensing Devices
The presence detectors that are most commonly
used in robotics safety are pressure mats and light curtains.
Floor mats (pressure sensitive mats) and light curtains (similar
to arrays of photocells) can be used to detect a person stepping
into a hazardous area near a robot. Proximity detectors
operating on electrical capacitance, ultrasonics, radio
frequency, laser, and
A-5
OSHA Instruction PUB 8-1.3 SEP 21, 1987 Office of
Science and Technology Assessment
television principles are currently undergoing
reliability testing in research laboratories because of
recognized limitations in their capability of detecting the
presence of personnel. Although some of these devices are
already available in the safety equipment marketplace, care must
be used in their selection to insure adequate safety and
reliability. At this time, such proximity detectors are not
recommended for such use unless a specific analysis confirms
their acceptability for the intended use.
Effective presence sensing devices stop all
motion of the robot if any part of a worker's body enters the
protected zone. Also, they are designed to be fail-safe so that
the occurrence of a failure within the device will leave it
unaffected or convert it into a mode in which its failed state
would not result in an accident. In some cases this means
deactivation of the robot. Factors which are considered in the
selection of such devices include spatial limitations of the
field, environmental conditions affecting the reliability of the
field, and sensing field interference due to robot operation.
5. Emergency Robot Braking
Dangerous robot movement is arrested by dynamic
braking systems rather than simple power cut-off. Such brakes
will counteract the effects of robot arm inertia. Cutting off
all power could create hazards such as a sudden dropping of a
robot's arm or flinging of a workpiece.
6. Audible and Visible Warning Systems
Audible and visible warning systems are not
acceptable safeguarding methods but may be used to enhance the
effectiveness of positive safeguards. The purposes of audible
and visible signals need to be easily recognizable.
CONTROL DEVICES
The following characteristics are essential for
control devices:
1. The main control panel is located outside the robot
system work envelope in sight of the robot.
2. Readily accessible emergency stops (palm buttons,
pull cords, etc.) are located in all zones where needed. These are
clearly situated in easily located positions and the position
identifications are a prominent part of personnel training. Emergency
stops override all other controls.
A-6
OSHA Instruction PUB 8-1.3 SEP 21, 1987 Office of
Science and Technology Assessment
3. The portable programming control device contains an
emergency stop.
4. Automatic stop capabilities are provided for
abnormal robot component speeds and robot traverses beyond the operating
envelope.
5. All control devices are clearly marked and labeled
as to device purpose. Actuating controls are designed to indicate the
robot's operating status.
6. Controls that initiate power or motion are
constructed and guarded against accidental operation.
7. Each robot is equipped with a separate circuit
breaker that can be locked only in the "off" position.
8. User-prompt displays are used to minimize human
errors.
9. The control system for a robot with lengthy
start-up time is designed to allow for the isolation of power to
components having mechanical motion from the power required to energize
the complete robot system.
10. Control systems are selected and designed so that
they prevent a robot from automatically restarting upon restoration of
power after electrical power failure. The systems also prevent hazardous
conditions in case of hydraulic, pneumatic or vacuum loss or change.
11. A robot system is designed so that it could be
moved manually on any of its axes without using the system drive power.
12. All control systems meet OSHA 29 CFR 1910 Subpart
S standards for electrical grounding, wiring, hazardous locations, and
related requirements.
INSTALLATION, MAINTENANCE AND PROGRAMMING
Good installation, maintenance, and programming
practices include the following:
1. The robot is installed in accordance with the
manufacturer's guidelines and applicable codes. Robots are compatible
with environmental conditions.
2. Power to the robot conforms to the manufacturer's
specifications.
3. The robot is secured to prevent vibration movement
and tip over.
4. Installation is such that no additional hazards are
created such as pinch points with fixed objects and robot components or
energized conductor contact with robot components.
A-7
OSHA Instruction PUB 8-1.3 SEP 21, 1987 Office of
Science and Technology Assessment
5. Signs and markings indicating the zones of movement
of the robot are displayed prominently on the robot itself and, if
possible, on floors and walls.
6. Stops are placed on the robot system's axes to
limit its motions under rated load and maximum speed conditions.
7. A lock-out procedure is established and enforced
for preventive maintenance or repair operations.
8. The robot manufacturer's preventive maintenance
schedule is followed rigorously.
9. A periodic check of all safety-critical equipment
and connections is established.
10. Stored energy devices, such as springs and
accumulators, are neutralized before robot servicing.
11. Only programmers have access to the work envelope
and full control of the robot when it is in the teach mode.
12. All robot motion initiated from a teach pendant
used by a programmer located within the robot work envelope is subject
to the current ANSI slow speed recommendation of 10 in/sec (250 mm/sec).
TRAINING
Effective accident prevention programs include
training. Some points to be considered in training programs include:
1. Managers and supervisors in facilities that use
robots are trained in the working aspects of robots so that they can set
and enforce a robotics safety policy from an informed viewpoint.
2. The employer insures that his or her company has a
written robotics safety policy that has been explained to all personnel
who will be working with robots. This safety policy states by name which
personnel are authorized to work with robots.
3. Robot programming and maintenance operations are
prohibited for persons other than those who have received adequate
training in hazard recognition and the control of robots.
A-8
OSHA Instruction PUB 8-1.3 SEP 21, 1987 Office of
Science and Technical Assessment
4. Robot operators receive adequate training in hazard
recognition and the control of robots and in the proper operating
procedure of the robot and associated equipment.
5. Training is commensurate with a trainee's needs and
includes the safeguarding method(s) and the required safe work practices
necessary for safe performance of the trainee's assigned job.
6. If it is necessary for an authorized person to be
within the work envelope while a robot is energized, for example during
a programming sequence, training is provided in the use of slow robot
operation speeds and hazardous location avoidance until the work is
completed. Such training also includes a review of emergency stops, and
a familiarization with the robot system's potentially hazardous energy
sources.
REFERENCES
- National Institute for Occupational Safety and
Health (NIOSH) Alert "Request for Assistance in preventing the Injury of
Workers by Robots." National Institute for Occupational Safety and
Health, Division of Safety Research, 944 Chestnut Ridge Road,
Morgantown, West Virginia 26505.
- American National Standards Institute (ANSI)
American National Safety Standard ANSI-RIA R15.06-1986, "Industrial
Robots and Industrial Robot Systems - Safety Requirements." American
National Standards Institute, Inc., 1430 Broadway, New York, New York
10018.
- Robotic Industries Association, 900 Victors Way,
P.O. Box 3724, Ann Arbor, Michigan 48106.
- Occupational Safety and Health Administration
publication 3067, Concepts and Techniques of Machine Safeguarding, U.S.
Department of Labor, 1980 (reprinted 1983). Superintendent of Documents,
U.S. Government Printing Office, Washington, DC 20210 |
INDUSTRIAL ROBOTS AND ROBOT SYSTEM SAFETY
FROM OSHA,
SECTION IV: CHAPTER 4
- INTRODUCTION.
Industrial robots are programmable multifunctional
mechanical devices designed to move material, parts, tools,
or specialized devices through variable programmed motions
to perform a variety of tasks. An industrial robot system
includes not only industrial robots but also any devices
and/or sensors required for the robot to perform its tasks
as well as sequencing or monitoring communication
interfaces.
Robots are generally used to perform unsafe, hazardous,
highly repetitive, and unpleasant tasks. They have many
different functions such as material handling, assembly, arc
welding, resistance welding, machine tool load and unload
functions, painting, spraying, etc. See
Appendix
IV:4-1 for common definitions.
Most robots are set up for an operation by the
teach-and-repeat technique. In this mode, a trained
operator (programmer) typically uses a portable control
device (a teach pendant) to teach a robot its task manually.
Robot speeds during these programming sessions are slow.
This instruction includes safety considerations necessary to
operate the robot properly and use it automatically in
conjunction with other peripheral equipment. This
instruction applies to fixed industrial robots and robot
systems only. See
Appendix
IV:4-2 for the systems that are
excluded.
- ACCIDENTS: PAST STUDIES.
- Studies in Sweden and Japan
indicate that many robot accidents do not occur
under normal operating conditions but, instead
during programming, program touch-up or
refinement, maintenance, repair, testing, setup, or
adjustment. During many of these operations the
operator, programmer, or corrective maintenance
worker may temporarily be within the robot's working
envelope where unintended operations could result in
injuries.
- Typical accidents have included
the following:
- A robot's arm functioned
erratically during a programming sequence and
struck the operator.
- A materials handling robot
operator entered a robot's work envelope during
operations and was pinned between the back end
of the robot and a safety pole.
- A fellow employee
accidentally tripped the power switch while a
maintenance worker was servicing an assembly
robot. The robot's arm struck the maintenance
worker's hand.
- ROBOT SAFEGUARDING.
- The proper selection of an
effective robotic safeguarding system should be
based upon a hazard analysis of the robot system's
use, programming, and maintenance operations. Among
the factors to be considered are the tasks a robot
will be programmed to perform, start-up
and command or programming procedures, environmental
conditions, location and installation requirements,
possible human errors, scheduled and unscheduled
maintenance, possible robot and system malfunctions,
normal mode of operation, and all personnel
functions and duties.
- An effective safeguarding system
protects not only operators but also engineers,
programmers, maintenance personnel, and any others
who work on or with robot systems and could be
exposed to hazards associated with a robot's
operation. A combination of safeguarding methods may
be used. Redundancy and backup systems are
especially recommended, particularly if a robot or
robot system is operating in hazardous conditions or
handling hazardous materials. The safeguarding
devices employed should not themselves constitute or
act as a hazard or curtail necessary vision or
viewing by attending human operators.
- TYPES AND CLASSIFICATION OF ROBOTS.
Industrial robots are available commercially in a wide range
of sizes, shapes, and configurations. They are designed and
fabricated with different design configurations and a
different number of axes or degrees of freedom. These
factors of a robot's design influence its working envelope
(the volume of working or reaching space). Diagrams of the
different robot design configurations are shown in Figure
IV: 4-1.
FIGURE IV:4-1. ROBOT ARM DESIGN
CONFIGURATIONS.
- SERVO AND NONSERVO.
All industrial robots are either servo or nonservo
controlled. Servo robots are controlled through the use
of sensors that continually monitor the robot's axes and
associated components for position and velocity. This
feedback is compared to pretaught information which has
been programmed and stored in the robot's memory.
Nonservo robots do not have the feedback capability, and
their axes are controlled through a system of mechanical
stops and limit switches.
- TYPE OF PATH GENERATED.
Industrial robots can be programmed from a distance to
perform their required and preprogrammed operations with
different types of paths generated through different
control techniques. The three different types of paths
generated are Point-to-Point Path,
Controlled Path, and Continuous Path.
- Point-to-Point Path.
Robots programmed and controlled in this manner are
programmed to move from one discrete point to
another within the robot's working envelope. In the
automatic mode of operation, the exact path taken by
the robot will vary slightly due to variations in
velocity, joint geometries, and point spatial
locations. This difference in paths is difficult to
predict and therefore can create a potential safety
hazard to personnel and equipment.
- Controlled Path.
The path or mode of movement ensures that the end of
the robot's arm will follow a predictable
(controlled) path and orientation as the robot
travels from point to point. The coordinate
transformations required for this hardware
management are calculated by the robot's control
system computer. Observations that result from this
type of programming are less likely to present a
hazard to personnel and equipment.
- Continuous Path.
A robot whose path is controlled by storing a large
number or close succession of spatial points in
memory during a teaching sequence is a continuous
path controlled robot. During this time, and while
the robot is being moved, the coordinate points in
space of each axis are continually monitored on a
fixed time base, e.g., 60 or more times per second,
and placed into the control system's computer
memory. When the robot is placed in the automatic
mode of operation, the program is replayed from
memory and a duplicate path is generated.
- ROBOT COMPONENTS.
Industrial robots have four major components: the
mechanical unit, power source, control system, and
tooling (Figure IV: 4-2).
- Mechanical Unit.
The robot's manipulative arm is the mechanical unit.
This mechanical unit is also comprised of a
fabricated structural frame with provisions for
supporting mechanical linkage and joints, guides,
actuators (linear or rotary), control valves, and
sensors. The physical dimensions, design, and
weight-carrying ability depend on application
requirements.
FIGURE IV:4-2. INDUSTRIAL
ROBOTS:
MAJOR COMPONENTS.
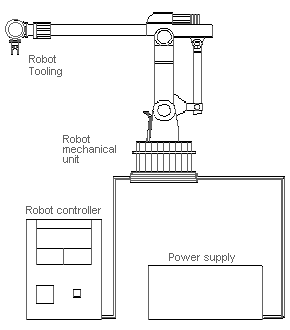
- Power Sources.
a. Energy is provided to various robot actuators
and their controllers as pneumatic, hydraulic, or
electrical power. The robot's drives are usually
mechanical combinations powered by these types of
energy, and the selection is usually based upon
application requirements. For example, pneumatic
power (low-pressure air) is used
generally for low weight carrying robots.
b. Hydraulic power transmission (high-pressure oil)
is usually used for medium to high force or weight
applications, or where smoother motion control can
be achieved than with pneumatics. Consideration
should be given to potential hazards of fires from
leaks if petroleum-based oils are used.
c. Electrically powered robots are the most
prevalent in industry. Either AC or DC electrical
power is used to supply energy to electromechanical
motor-driven actuating mechanisms and
their respective control systems. Motion control is
much better, and in an emergency an electrically
powered robot can be stopped or powered down more
safely and faster than those with either pneumatic
or hydraulic power.
- CONTROL SYSTEMS.
- Either auxiliary computers or
embedded microprocessors are used for practically
all control of industrial robots today. These
perform all of the required computational functions
as well as interface with and control associated
sensors, grippers, tooling, and other associated
peripheral equipment. The control system performs
the necessary sequencing and memory functions for
on-line sensing, branching, and
integration of other equipment. Programming of the
controllers can be done on-line or at
remote off-line control stations with
electronic data transfer of programs by cassette,
floppy disc, or telephone modem.
- Self-diagnostic capability for
troubleshooting and maintenance greatly reduces
robot system downtime. Some robot controllers have
sufficient capacity, in terms of computational
ability, memory capacity, and input-output
capability to serve also as system controllers and
handle many other machines and processes.
Programming of robot controllers and systems has not
been standardized by the robotics industry;
therefore, the manufacturers use their own
proprietary programming languages which require
special training of personnel.
- ROBOT PROGRAMMING BY TEACHING
METHODS. A program consists of
individual command steps which state either the position
or function to be performed, along with other
informational data such as speed, dwell or delay times,
sample input device, activate output device, execute,
etc.
When establishing a robot program, it is necessary to
establish a physical or geometrical relationship between
the robot and other equipment or work to be serviced by
the robot. To establish these coordinate points
precisely within the robot's working envelope, it is
necessary to control the robot manually and physically
teach the coordinate points. To do this as well as
determine other functional programming information,
three different teaching or programming techniques are
used: lead-through, walk-through,
and off-line.
- Lead-Through Programming or
Teaching. This method of
teaching uses a proprietary teach pendant (the
robot's control is placed in a "teach" mode), which
allows trained personnel physically to lead the
robot through the desired sequence of events by
activating the appropriate pendant button or switch.
Position data and functional information are
"taught" to the robot, and a new program is written
(Figure IV:4-3). The teach pendant can
be the sole source by which a program is
established, or it may be used in conjunction with
an additional programming console and/or the robot's
controller. When using this technique of teaching or
programming, the person performing the teach
function can be within the robot's working envelope,
with operational safeguarding devices deactivated or
inoperative.
FIGURE IV:4-3. ROBOT
LEAD-THROUGH PROGRAMMING OR TEACHING.
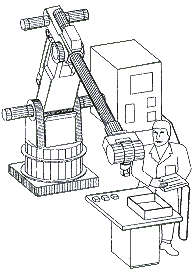
- Walk-Through Programming or
Teaching. A person doing
the teaching has physical contact with the robot arm
and actually gains control and walks the robot's arm
through the desired positions within the working
envelope (Figure IV:4-4).
FIGURE IV:4-4. WALK-THROUGH
PROGRAMMING OR TEACHING.
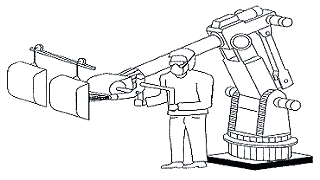
During this time, the robot's controller is scanning
and storing coordinate values on a fixed time basis.
When the robot is later placed in the automatic mode
of operation, these values and other functional
information are replayed and the program run as it
was taught. With the walk-through
method of programming, the person doing the teaching
is in a potentially hazardous position because the
operational safeguarding devices are deactivated or
inoperative.
Off-Line Programming. The programming
establishing the required sequence of functional and
required positional steps is written on a remote
computer console (Figure IV:4-5). Since
the console is distant from the robot and its
controller, the written program has to be
transferred to the robot's controller and precise
positional data established to achieve the actual
coordinate information for the robot and other
equipment. The program can be transferred directly
or by cassette or floppy discs. After the program
has been completely transferred to the robot's
controller, either the lead-through or
walk-through technique can be used for
obtaining actual positional coordinate information
for the robot's axes.
FIGURE IV:4-5. OFF-LINE
PROGRAMMING OR TEACHING.
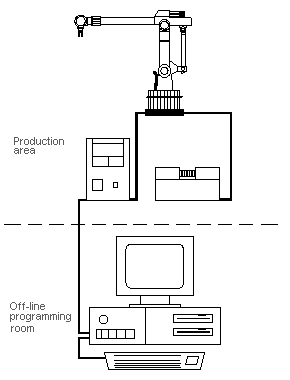
When programming robots with any of the three
techniques discussed above, it is generally required
that the program be verified and slight
modifications in positional information made. This
procedure is called program touch-up
and is normally carried out in the teach mode of
operation. The teacher manually leads or walks the
robot through the programmed steps. Again, there are
potential hazards if safeguarding devices are
deactivated or inoperative.
- DEGREES OF FREEDOM.
Regardless of the configuration of a robot, movement
along each axis will result in either a rotational
or a translational movement. The number of axes of
movement (degrees of freedom) and their arrangement,
along with their sequence of operation and
structure, will permit movement of the robot to any
point within its envelope. Robots have three arm
movements (up-down, in-out,
side-to-side). In addition, they can
have as many as three additional wrist movements on
the end of the robot's arm: yaw (side to side),
pitch (up and down), and rotational (clockwise and
counterclockwise).
- HAZARDS.
The operational characteristics of robots can be
significantly different from other machines and equipment.
Robots are capable of high-energy (fast or powerful)
movements through a large volume of space even beyond the
base dimensions of the robot (see Figure IV:4-6).
The pattern and initiation of movement of the robot is
predictable if the item being "worked" and the environment
are held constant. Any change to the object being worked
(i.e., a physical model change) or the environment can
affect the programmed movements.
FIGURE IV:4-6. A ROBOT'S WORK
ENVELOPE.
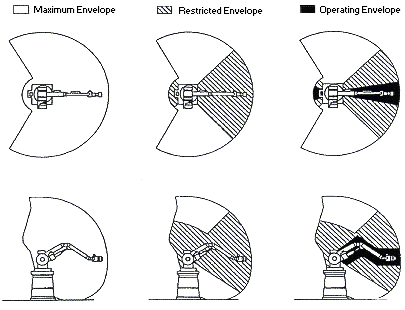
Some maintenance and programming personnel may be required
to be within the restricted envelope while power is
available to actuators. The restricted envelope of the robot
can overlap a portion of the restricted envelope of other
robots or work zones of other industrial machines and
related equipment. Thus, a worker can be hit by one robot
while working on another, trapped between them or peripheral
equipment, or hit by flying objects released by the gripper.
A robot with two or more resident programs can find the
current operating program erroneously calling another
existing program with different operating parameters such as
velocity, acceleration, or deceleration, or position within
the robot's restricted envelope. The occurrence of this
might not be predictable by maintenance or programming
personnel working with the robot. A component malfunction
could also cause an unpredictable movement and/or robot arm
velocity.
Additional hazards can also result from the malfunction of,
or errors in, interfacing or programming of other process or
peripheral equipment. The operating changes with the process
being performed or the breakdown of conveyors, clamping
mechanisms, or process sensors could cause the robot to
react in a different manner.
- TYPES OF ACCIDENTS.
Robotic incidents can be grouped into four categories: a
robotic arm or controlled tool causes the accident,
places an individual in a risk circumstance, an
accessory of the robot's mechanical parts fails, or the
power supplies to the robot are uncontrolled.
- Impact or Collision Accidents.
Unpredicted movements, component malfunctions, or
unpredicted program changes related to the robot's
arm or peripheral equipment can result in contact
accidents.
- Crushing and Trapping
Accidents. A worker's limb
or other body part can be trapped between a robot's
arm and other peripheral equipment, or the
individual may be physically driven into and crushed
by other peripheral equipment.
- Mechanical Part Accidents.
The breakdown of the robot's drive components,
tooling or end-effector, peripheral equipment, or
its power source is a mechanical accident. The
release of parts, failure of gripper mechanism, or
the failure of end-effector power tools
(e.g., grinding wheels, buffing wheels, deburring
tools, power screwdrivers, and nut runners) are a
few types of mechanical failures.
- Other Accidents.
Other accidents can result from working with robots.
Equipment that supplies robot power and control
represents potential electrical and pressurized
fluid hazards. Ruptured hydraulic lines could create
dangerous high-pressure cutting streams
or whipping hose hazards. Environmental accidents
from arc flash, metal spatter, dust,
electromagnetic, or radio-frequency
interference can also occur. In addition, equipment
and power cables on the floor present tripping
hazards.
- SOURCES OF HAZARDS.
The expected hazards of machine to humans can be
expected with several additional variations, as follows.
- Human Errors.
Inherent prior programming, interfacing activated
peripheral equipment, or connecting live
input-output sensors to the microprocessor or
a peripheral can cause dangerous, unpredicted
movement or action by the robot from human error.
The incorrect activation of the "teach pendant" or
control panel is a frequent human error. The
greatest problem, however, is overfamiliarity with
the robot's redundant motions so that an
individual places himself in a hazardous position
while programming the robot or performing
maintenance on it.
- Control Errors.
Intrinsic faults within the control system of the
robot, errors in software, electromagnetic
interference, and radio frequency interference are
control errors. In addition, these errors can occur
due to faults in the hydraulic, pneumatic, or
electrical subcontrols associated with the robot or
robot system.
- Unauthorized Access.
Entry into a robot's safeguarded area is hazardous
because the person involved may not be familiar with
the safeguards in place or their activation status.
- Mechanical Failures.
Operating programs may not account for cumulative
mechanical part failure, and faulty or unexpected
operation may occur.
- Environmental Sources.
Electromagnetic or radio-frequency interference
(transient signals) should be considered to exert an
undesirable influence on robotic operation and
increase the potential for injury to any person
working in the area. Solutions to environmental
hazards should be documented prior to equipment
start-up.
- Power Systems.
Pneumatic, hydraulic, or electrical power sources
that have malfunctioning control or transmission
elements in the robot power system can disrupt
electrical signals to the control and/or
power-supply lines. Fire risks are increased
by electrical overloads or by use of flammable
hydraulic oil. Electrical shock and release of
stored energy from accumulating devices also can be
hazardous to personnel.
- Improper Installation.
The design, requirements, and layout of equipment,
utilities, and facilities of a robot or robot
system, if inadequately done, can lead to inherent
hazards.
- INVESTIGATION GUIDELINES.
- MANUFACTURED, REMANUFACTURED, AND
REBUILT ROBOTS.
- All robots should meet minimum
design requirements to ensure safe operation by the
user. Consideration needs to be given to a number of
factors in designing and building the robots to
industry standards. If older or obsolete robots are
rebuilt or remanufactured, they should be upgraded
to conform to current industry standards.
- Every robot should be designed,
manufactured, remanufactured, or rebuilt with safe
design and manufacturing considerations. Improper
design and manufacture can result in hazards to
personnel if minimum industry standards are not
conformed to on mechanical components, controls,
methods of operation, and other required information
necessary to insure safe and proper operating
procedures. To ensure that robots are designed,
manufactured, remanufactured, and rebuilt to ensure
safe operation, it is recommended that they comply
with Section 4 of the ANSI/RIA R15.06-1992
standard for Manufacturing, Remanufacture, and
Rebuild of Robots.
- INSTALLATION.
- A robot or robot system should be
installed by the users in accordance with the
manufacturer's recommendations and in conformance to
acceptable industry standards. Temporary
safeguarding devices and practices should be used to
minimize the hazards associated with the
installation of new equipment. The facilities,
peripheral equipment, and operating conditions which
should be considered are:
- Installation specifications;
- Physical facilities;
- Electrical facilities;
- Action of peripheral
equipment integrated with the robot;
- Identification requirements;
- Control and emergency stop
requirements; and
- Special robot operating
procedures or conditions.
- To ensure safe operating
practices and safe installation of robots and robot
systems, it is recommended that the minimum
requirements of Section 5 of the ANSI/RIA
R15.06-1992, Installation of Robots and Robot
Systems be followed. In addition, OSHA's
Lockout/Tagout
standards (29 CFR
1910.147 and
1910.333) must be followed for servicing and
maintenance.
- CONTROL AND SAFEGUARDING
PERSONNEL.
For the planning stage, installation, and subsequent
operation of a robot or robot system, one should consider
the following.
- RISK ASSESSMENT.
At each stage of development of the robot and robot
system a risk assessment should be performed. There are
different system and personnel safeguarding requirements
at each stage. The appropriate level of safeguarding
determined by the risk assessment should be applied. In
addition, the risk assessments for each stage of
development should be documented for future reference.
- SAFEGUARDING DEVICES.
Personnel should be safeguarded from hazards associated
with the restricted envelope (space) through the use of
one or more safeguarding devices:
- Mechanical limiting devices;
- Nonmechanical limiting devices;
- Presence-sensing safeguarding
devices;
- Fixed barriers (which prevent
contact with moving parts); and
- Interlocked barrier guards.
- AWARENESS DEVICES.
Typical awareness devices include chain or rope barriers
with supporting stanchions or flashing lights, signs,
whistles, and horns. They are usually used in
conjunction with other safeguarding devices.
- SAFEGUARDING THE TEACHER.
Special consideration must be given to the teacher or
person who is programming the robot. During the teach
mode of operation, the person performing the teaching
has control of the robot and associated equipment and
should be familiar with the operations to be programmed,
system interfacing, and control functions of the robot
and other equipment. When systems are large and complex,
it can be easy to activate improper functions or
sequence functions improperly. Since the person doing
the training can be within the robot's restricted
envelope, such mistakes can result in accidents.
Mistakes in programming can result in unintended
movement or actions with similar results. For this
reason, a restricted speed of 250 mm/§ or 10 in/§ should
be placed on any part of the robot during training to
minimize potential injuries to teaching personnel.
Several other safeguards are suggested in the ANSI/RIA
R15.06-1992 standard to reduce the hazards associated
with teaching a robotic system.
- OPERATOR SAFEGUARDS.
The system operator should be protected from all hazards
during operations performed by the robot. When the robot
is operating automatically, all safeguarding devices
should be activated, and at no time should any part of
the operator's body be within the robot's safeguarded
area.
For additional operator safeguarding suggestions, see
the ANSI/RIA R15.06-1992 standard, Section 6.6.
- ATTENDED CONTINUOUS OPERATION.
When a person is permitted to be in or near the robots
restricted envelope to evaluate or check the robots
motion or other operations, all continuous operation
safeguards must be in force. During this operation, the
robot should be at slow speed, and the operator would
have the robot in the teach mode and be fully in control
of all operations.
Other safeguarding requirements are suggested in the
ANSI/RIA R15.06-1992 standard, Section 6.7.
- MAINTENANCE AND REPAIR PERSONNEL.
Safeguarding maintenance and repair personnel is very
difficult because their job functions are so varied.
Troubleshooting faults or problems with the robot,
controller, tooling, or other associated equipment is
just part of their job. Program touchup is another of
their jobs as is scheduled maintenance, and adjustments
of tooling, gages, recalibration, and many other types
of functions.
While maintenance and repair is being performed, the
robot should be placed in the manual or teach mode, and
the maintenance personnel perform their work within the
safeguarded area and within the robots restricted
envelope. Additional hazards are present during this
mode of operation because the robot system safeguards
are not operative.
To protect maintenance and repair personnel,
safeguarding techniques and procedures as stated in the
ANSI/RIA R15.06-1992 standard, Section 6.8,
are recommended.
- MAINTENANCE.
Maintenance should occur during the regular and periodic
inspection program for a robot or robot system. An
inspection program should include, but not be limited
to, the recommendations of the robot manufacturer and
manufacturer of other associated robot system equipment
such as conveyor mechanisms, parts feeders, tooling,
gages, sensors, and the like.
These recommended inspection and maintenance programs
are essential for minimizing the hazards from component
malfunction, breakage, and unpredicted movements or
actions by the robot or other system equipment. To
ensure proper maintenance, it is recommended that
periodic maintenance and inspections be documented along
with the identity of personnel performing these tasks.
- SAFETY TRAINING.
Personnel who program, operate, maintain, or repair
robots or robot systems should receive adequate safety
training, and they should be able to demonstrate their
competence to perform their jobs safely. Employers can
refer to OSHA's publication 2254 (Revised), "Training
Requirements in OSHA Standards and Training Guidelines."
- GENERAL REQUIREMENTS.
To ensure minimum safe operating practices and
safeguards for robots and robot systems covered by this
instruction, the following sections of the ANSI/RIA
R15.06-1992 must also be considered:
- Section 6 - Safeguarding
Personnel;
- Section 7 - Maintenance of Robots
and Robot Systems;
- Section 8 - Testing and Start-up
of Robots and Robot Systems; and
- Section 9 - Safety Training of
Personnel.
Robots or robotic systems must comply with the following
regulations: Occupational Safety and Health
Administration, OSHA 29 CFR
1910.333, Selection and Use of Work Practices, and
OSHA 29 CFR Part
1910.147, The Control of Hazardous Energy (Lockout/Tagout).
APPENDIX IV:4-1. GLOSSARY FOR ROBOTICS AND ROBOTIC SYSTEMS.
Actuator A power mechanism used to effect motion of the
robot; a device that converts electrical, hydraulic, or
pneumatic energy into robot motion.
Application Program The set of instructions that
defines the specific intended tasks of robots and robot systems.
This program may be originated and modified by the robot user.
Attended Continuous Operation The time when robots are
performing (production) tasks at a speed no greater than slow
speed through attended program execution.
Attended Program Verification The time when a person
within the restricted envelope (space) verifies the robot's
programmed tasks at programmed speed.
Automatic Mode The robot state in which automatic
operation can be initiated.
Automatic Operation The time during which robots are
performing programmed tasks through unattended program
execution.
Awareness Barrier Physical and/or visual means that
warns a person of an approaching or present hazard.
Awareness Signal A device that warns a person of an
approaching or present hazard by means of audible sound or
visible light.
Axis The line about which a rotating body (such as a
tool) turns.
Barrier A physical means of separating persons from the
restricted envelope (space).
Control Device Any piece of control hardware providing
a means for human intervention in the control of a robot or
robot system, such as an emergency-stop button, a
start button, or a selector switch.
Control Program The inherent set of control
instructions that defines the capabilities, actions and
responses of the robot system. This program is usually not
intended to be modified by the user.
Coordinated Straight Line Motion Control wherein the
axes of the robot arrive at their respective end points
simultaneously, giving a smooth appearance to the motion.
Control wherein the motions of the axes are such that the Tool
Center Point (TCP) moves along a prespecified type of path
(line, circle, etc.)
Device Any piece of control hardware such as an
emergency-stop button, selector switch, control pendant,
relay, solenoid valve, sensor, etc.
Drive Power The energy source or sources for the robot
actuators.
Emergency Stop The operation of a circuit using
hardware-based components that overrides all other robot
controls, removes drive power from the robot actuators, and
causes all moving parts to stop.
Enabling Device A manually operated device that permits
motion when continuously activated. Releasing the device stops
robot motion and motion of associated equipment that may present
a hazard.
End-effector An accessory device or tool specifically
designed for attachment to the robot wrist or tool mounting
plate to enable the robot to perform its intended task.
(Examples may include gripper, spot-weld gun,
arc-weld gun, spray- paint gun, or any other
application tools.)
Energy Source Any electrical, mechanical, hydraulic,
pneumatic, chemical, thermal, or other source.
Envelope (Space), Maximum The volume of space
encompassing the maximum designed movements of all robot parts
including the end-effector, workpiece, and
attachments.
Restricted Envelope (Space) That portion of the maximum
envelope to which a robot is restricted by limiting devices. The
maximum distance that the robot can travel after the limiting
device is actuated defines the boundaries of the restricted
envelope (space) of the robot.
NOTE: The safeguarding interlocking logic and robot
program may redefine the restricted envelope (space) as the
robot performs its application program. (See Appendix D of the
ANSI/RIA R15.06-1992 Specification).
Operating Envelope (Space) That portion of the
restricted envelope (space) that is actually used by the robot
while performing its programmed motions.
Hazard A situation that is likely to cause physical
harm.
Hazardous Motion Any motion that is likely to cause
personal physical harm.
Industrial Equipment Physical apparatus used to perform
industrial tasks, such as welders, conveyors, machine tools,
fork trucks, turn tables, positioning tables, or robots.
Industrial Robot A reprogrammable, multifunctional
manipulator designed to move material, parts, tools, or
specialized devices through variable programmed motions for the
performance of a variety of tasks.
Industrial Robot System A system that includes
industrial robots, the end-effectors, and the devices and
sensors required for the robots to be taught or programmed, or
for the robots to perform the intended automatic operations, as
well as the communication interfaces required for interlocking,
sequencing, or monitoring the robots.
Interlock An arrangement whereby the operation of one
control or mechanism brings about or prevents the operation of
another.
Joint Motion A method for coordinating the movement of
the joints such that all joints arrive at the desired location
simultaneously.
Limiting Device A device that restricts the maximum
envelope (space) by stopping or causing to stop all robot motion
and is independent of the control program and the application
programs.
Maintenance The act of keeping the robots and robot
systems in their proper operating condition.
Mobile Robot A self-propelled and self-contained robot
that is capable of moving over a mechanically unconstrained
course.
Muting The deactivation of a presence-sensing
safeguarding device during a portion of the robot cycle.
Operator The person designated to start, monitor, and
stop the intended productive operation of a robot or robot
system. An operator may also interface with a robot for
productive purposes.
Pendant Any portable control device, including teach
pendants, that permits an operator to control the robot from
within the restricted envelope (space) of the robot.
Presence-Sensing Safeguarding Device A device designed,
constructed, and installed to create a sensing field or area to
detect an intrusion into the field or area by personnel, robots,
or other objects.
Program
- (noun) A sequence of instructions to be
executed by the computer or robot controller to control a
robot or robot system.
- (verb) to furnish (a computer) with a
code of instruction.
- (verb) to teach a robot system a specific
set of movements and instructions to accomplish a task.
Rebuild To
restore the robot to the original specifications of the
manufacturer, to the extent possible.
Remanufacture To upgrade or modify robots to the
revised specifications of the manufacturer and applicable
industry standards.
Repair To restore robots and robot systems to operating
condition after damage, malfunction, or wear.
Robot Manufacturer A company or business involved in
either the design, fabrication, or sale of robots, robot
tooling, robotic peripheral equipment or controls, and
associated process ancillary equipment.
Robot System Integrator A company or business who
either directly or through a subcontractor will assume
responsibility for the design, fabrication, and integration of
the required robot, robotic peripheral equipment, and other
required ancillary equipment for a particular robotic
application.
Safeguard A barrier guard, device, or safety procedure
designed for the protection of personnel.
Safety Procedure An instruction designed for the
protection of personnel.
Sensor A device that responds to physical stimuli (such
as heat, light, sound, pressure, magnetism, motion, etc.) and
transmits the resulting signal or data for providing a
measurement, operating a control, or both.
Service To adjust, repair, maintain, and make fit for
use.
Single Point of Control The ability to operate the
robot such that initiation or robot motion from one source of
control is possible only from that source and cannot be
overridden from another source.
Slow Speed Control A mode of robot motion control where
the velocity of the robot is limited to allow persons sufficient
time either to withdraw the hazardous motion or stop the robot.
Start-up Routine application of drive power to the
robot or robot system.
Start-up, Initial Initial drive power application to
the robot or robot system after one of the following events:
- Manufacture or modification;
- Installation or reinstallation;
- Programming or program editing; and
- Maintenance or repair.
Teach The generation and storage
of a series of positional data points effected by moving the
robot arm through a path of intended motions.
Teach Mode The control state that allows the generation
and storage of positional data points effected by moving the
robot arm through a path of intended motions.
Teacher A person who provides the robot with a specific
set of instructions to perform a task.
Tool Center Point (TCP) The origin of the tool
coordinate system.
User A company, business, or person who uses robots and
who contracts, hires, or is responsible for the personnel
associated with robot operation.
APPENDIX IV: 4-2. OTHER ROBOTIC SYSTEMS
NOT COVERED BY THIS CHAPTER.
Service robots are machines that extend human
capabilities.
Automatic guided-vehicle systems are advanced
material-handling or conveying systems that involve a driverless
vehicle which follows a guide-path.
Undersea and space robots include in addition to the
manipulator or tool that actually accomplishes a task, the
vehicles or platforms that transport the tools to the site.
These vehicles are called remotely operated vehicles (ROV's) or
autonomous undersea vehicles (AUV's); the feature that
distinguishes them is, respectively, the presence or absence of
an electronics tether that connects the vehicle and surface
control station.
Automatic storage and retrieval systems are storage
racks linked through automatically controlled conveyors and an
automatic storage and retrieval machine or machines that ride on
floor-mounted guide rails and power-driven
wheels.
Automatic conveyor and shuttle systems are comprised of
various types of conveying systems linked together with various
shuttle mechanisms for the prime purpose of conveying materials
or parts to prepositioned and predetermined locations
automatically.
Teleoperators are robotic devices comprised of sensors
and actuators for mobility and/or manipulation and are
controlled remotely by a human operator.
Mobile robots are freely moving automatic programmable
industrial robots.
Prosthetic robots are programmable manipulators or
devices for missing human limbs.
Numerically controlled machine tools are operated by a
series of coded instructions comprised of numbers, letters of
the alphabet, and other symbols. These are translated into
pulses of electrical current or other output signals that
activate motors and other devices to run the machine.
|
|
|